When it comes to aggregate production, bigger isn’t always better. While states like Texas and California garner much attention due to their large geographical size and abundant resources, smaller states like Connecticut and New Jersey consistently show impressive aggregate production figures. But how is it possible for these smaller states to compete with the bigger players? The answer lies in a combination of factors, including efficiency, quality, and strategic location.
Efficiency: Making the Most Out of What You've Got
Connecticut, for example, is a small state with a total aggregate production of 14,991,416. What makes this number truly noteworthy is the market share of the top producers, with CRH PLC holding 43%, O & G Industries Inc at 8%, and Rawson Materials Inc. at 7%. Despite having limited land area and resources, these companies have honed their operations to an art, squeezing every bit of value out of the materials they produce.
Quality Over Quantity: The Caliber of Aggregates
In both Connecticut and New Jersey, the quality of aggregates is another key factor that allows these states to punch above their weight. Superior geological formations offer high-quality materials that often fetch higher market prices, making these states competitive in a crowded market. New Jersey has an abundance of quality sand and gravel resources, while Connecticut has quality crushed stone available throughout narrow geological bands throughout the state. Both are illustrated within the Mineralocity Aggregates platform and shown in the screenshots below:
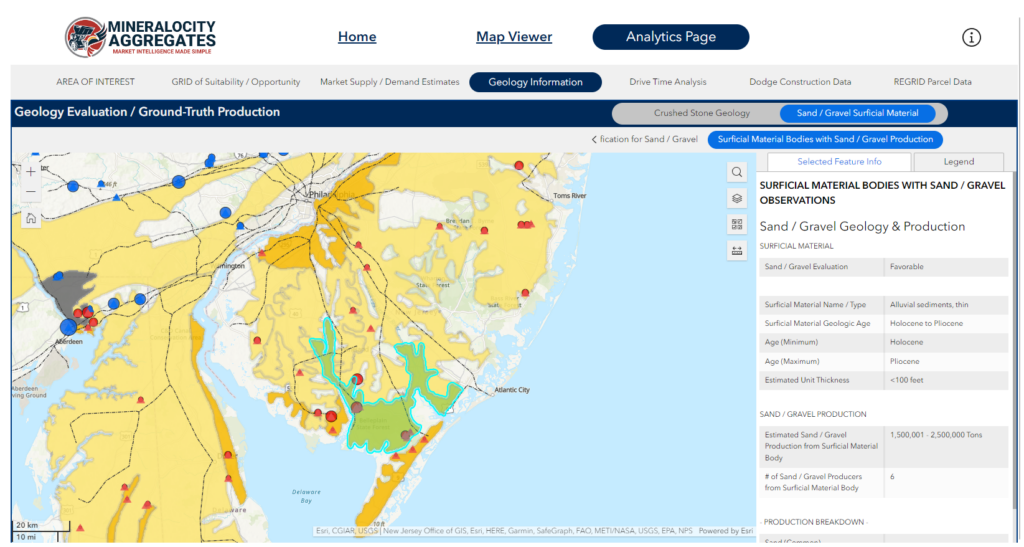
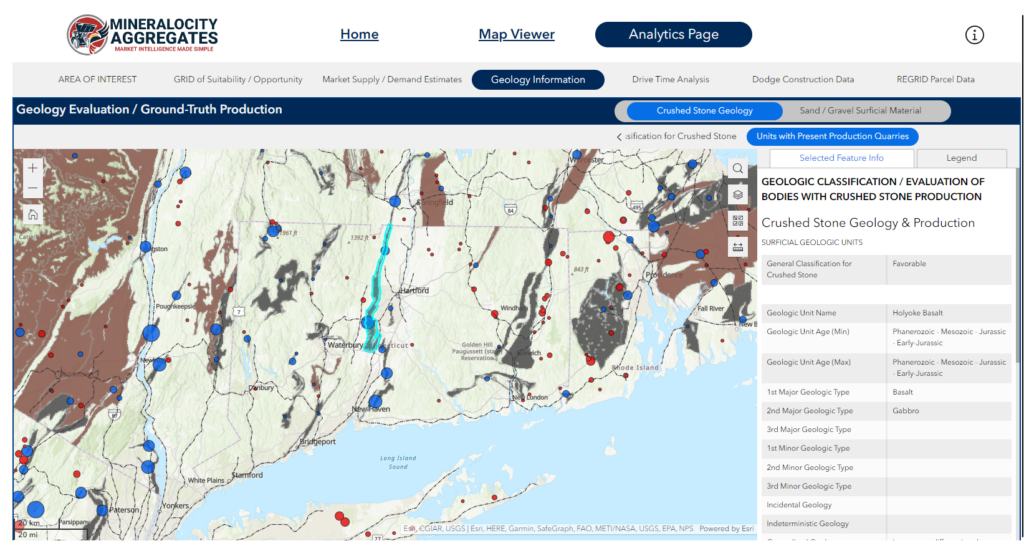
Strategic Exporting: Leveraging Geographic Location and Economic Relationships
When discussing the aggregate production success of states like Connecticut and New Jersey, it’s important to understand their economic ties with neighboring regions. This interconnectedness not only adds another layer to their capability to produce and export aggregates but also makes them key players in the broader economic landscape.
New York’s Economic Magnetism
Both New Jersey and Connecticut are deeply connected to New York, particularly New York City, the economic hub of the region. With a large commuting population traveling for work between these states and the city, there’s a constant flow of economic activity. Companies such as MetLife, Prudential Financial, and Johnson & Johnson are Fortune 500 entities headquartered in New York City, but they also have significant operations and workforce in New Jersey and Connecticut. Moreover, New Jersey serves as a major transportation hub for New York, and the Port of Newark is among the busiest ports in the United States. This facilitates the smooth transfer of aggregate materials to various markets.
Pennsylvania: The Border Trade Advantage
Pennsylvania is another vital partner that shares long borders with New Jersey and Connecticut. As major suppliers of goods and services, including aggregates, to Pennsylvania-based businesses, these states experience a beneficial economic interchange. The shared borders also mean that Pennsylvania is a notable tourist destination for people residing in both New Jersey and Connecticut, which indirectly boosts the aggregate demand for infrastructure projects. It should be noted that Pennsylvania is also a major aggregate producer for its size with an annual estimated 2022 production of over 105 million tons.
Massachusetts: The Sectoral Synergy
Though smaller in size, Massachusetts commands significant economic importance. It is home to corporations that are giants in sectors such as life sciences, technology, and finance, like Boston Scientific and Fidelity Investments. Collaborative efforts between Massachusetts and New Jersey or Connecticut businesses are frequent, particularly in these specialized sectors. This kind of cross-border investment and collaboration extends to the aggregate industry, where the high-quality aggregates from Connecticut and New Jersey find lucrative markets.
Rhode Island: The Small Giant
Rhode Island may be the smallest New England state, but it has a significant economic footprint, hosting Fortune 500 companies like CVS Health and The Providence Journal. The sectors of manufacturing, tourism, and healthcare see particularly strong collaborations between Rhode Island and New Jersey or Connecticut businesses, creating an avenue for aggregate material exchange and investment.
Beyond the Borders
While the closest and most robust economic relationships are with neighboring New England states, New Jersey and Connecticut are not limited to these borders. Their reach extends nationally and even globally, but it’s this local interconnectedness that significantly fuels their impressive aggregate production figures.
The Future is Bright: Sustainable Practices
Both states have adopted sustainable aggregate production methods, such as recycling old concrete into new aggregate, that not only reduce the environmental impact but also contribute to efficiency.
Conclusion
The tale of Connecticut and New Jersey serves as a lesson that size doesn’t always matter. It’s a mix of efficiency, quality, and location that makes these states stand out. If you’re intrigued by these insights and want to know who else is making waves in the aggregate industry, don’t miss our Top Aggregate Producers Report for 2023. Discover how companies like Mineralocity Aggregates are shaping the future of aggregate production.
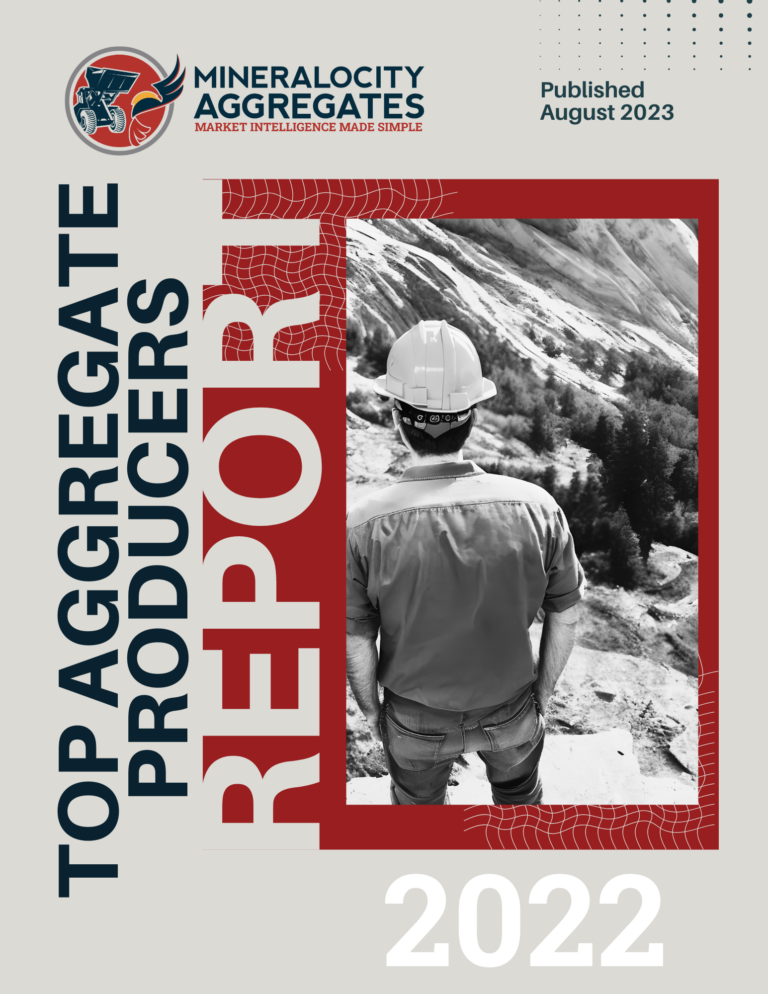
Unlock exclusive, groundbreaking market data with the 2022 Top Aggregate Producers Report. Don't miss out!
Gain a competitive edge with our 2022 Top Aggregate Producers Report! Get exclusive market share data on top producers in each U.S. state with market trends to strategize effectively. A must-have for every industry player!