Whether you’re an established aggregate producer looking to expand, or an entrepreneur venturing into the industry, discovering and evaluating greenfield sites for their usable acreage is a critical step in growing your aggregate business. Greenfield sites—those lands untouched by previous mining—are potential goldmines. But unlocking their potential calls for a systematic and strategic approach. Let’s explore the step-by-step process of how to determine the usable acreage of a greenfield site for your aggregate business.
Securing Ample Usable Acreage: The Bedrock of Successful Aggregate Mining
The decision to lease, option, or purchase a property for aggregate mining is a significant one, and ensuring sufficient usable acreage is fundamental to its success. This is not just about having enough space to house your operations, but about securing the long-term viability of your enterprise.
In aggregate mining, the rule of thumb is that the operation requires 100 acres or more, depending on its size and production rate. This may seem expansive, but the large footprint is justified when you delve into the intricacies of the mining process. The extraction areas, processing facilities, stockpiles, overburden storage, settling ponds, office spaces, haul roads, buffer zones for environmental and safety considerations, and even potential future expansion all contribute to the space requirements.
Moreover, aggregate mining is a time-intensive operation. A site may be active for several decades, which means planning should extend far into the future. Securing enough acreage from the start allows for the evolution and growth of the operation, accommodating changes in demand, technology, and operational strategies.
In some cases, a smaller footprint may be possible with careful planning and under ideal conditions. However, these instances tend to be the exception rather than the rule. Operating on a site with insufficient acreage could lead to operational constraints, inefficient production, and environmental or regulatory complications.
Thus, ensuring enough usable acreage is not just about the present, but an investment in the future – a proactive step to maintain the resilience and profitability of your aggregate mining operation. Always remember, when it comes to aggregate mining, securing adequate land is securing your business’s success.
It’s essential to understand that not all land within a property will be usable for mining operations. The overall size of a property can be deceiving, as various factors may reduce the usable acreage for actual mining activities. Constraints can come from environmental elements, such as wetlands, which require specific buffers, or built structures and infrastructure that also require a safe distance. Other limitations can stem from local regulations and community considerations, which may restrict operations in certain areas. Therefore, when considering a property for aggregate mining, it’s crucial to conduct a thorough evaluation to identify these potential hindrances and accurately estimate the truly usable acreage. This careful planning ensures that your mining operation will have the space it needs to operate efficiently and responsibly, now and in the future.
Step 1: Marking Territory

Your journey begins with identifying the property lines of the potential site. A thorough survey of the site’s boundaries provides a crucial starting point for assessing its usability. Typically, a buffer of around 100 feet is maintained from the property line, although this may vary based on location-specific rules and regulations. This buffer ensures that mining operations don’t infringe on neighboring properties or local jurisdictions and maintains an aesthetic and functional barrier between the mine and its surroundings.
Step 2: Respecting Wetlands and other Environmentally Sensitive Areas
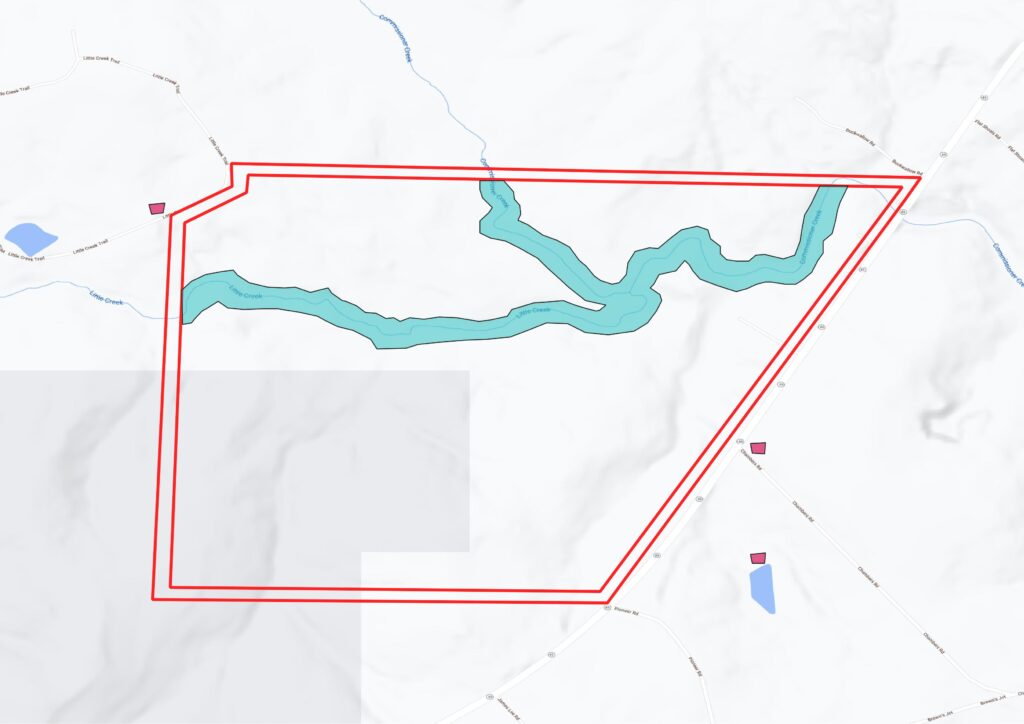
Next, we pay attention to the site’s natural features, particularly wetlands, which are recognized for their vital role in maintaining ecological balance. Mapping out wetlands, guided by resources such as the National Wetlands Map, and establishing a buffer of roughly 125 feet around them is a key aspect of the evaluation. The wetland areas, along with their buffer zones, are earmarked as non-usable due to environmental regulations and the essential need for their preservation. In some cases, these wetlands can be disturbed and mitigated through credits and other means, but this process can be difficult and expensive and is best avoided where possible.
Step 3: Roadblocks and Powerlines

Infrastructure, like roads and powerlines, can pose unique challenges to aggregate operations. They require careful mapping and buffers of about 100 feet. State and county roads or powerlines running through the site can dictate operational areas, making those regions within the buffer non-usable for mining.
Step 4: Factoring in Blasting Buffers for Quarries
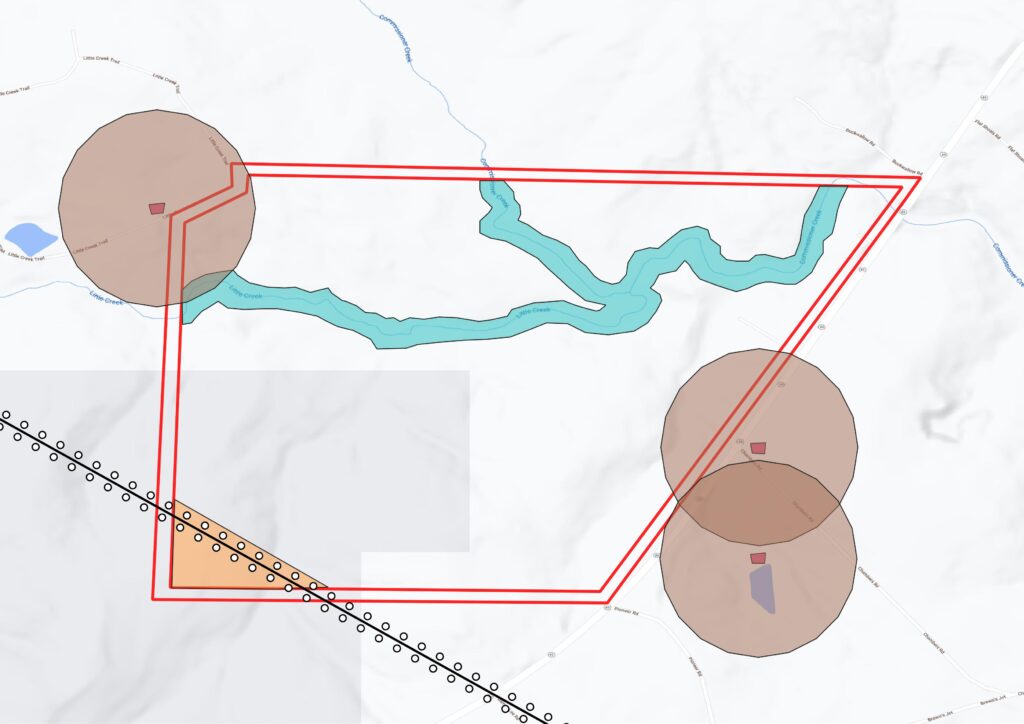
After mapping out the non-usable areas and accounting for all buffers, the remaining area might appear ready for mining. However, there’s another crucial factor to consider: blasting buffers. Aggregate quarrying operations often require blasting, which necessitates further safety precautions.
Around every structure on and around the site—homes, buildings, garages, sheds, etc.—a radius (often 1,000 feet, subject to local regulations) is drawn. The areas within these radii cannot be used for mining due to the risks and vibrations associated with blasting.
Step 5: Maximizing Usable Space
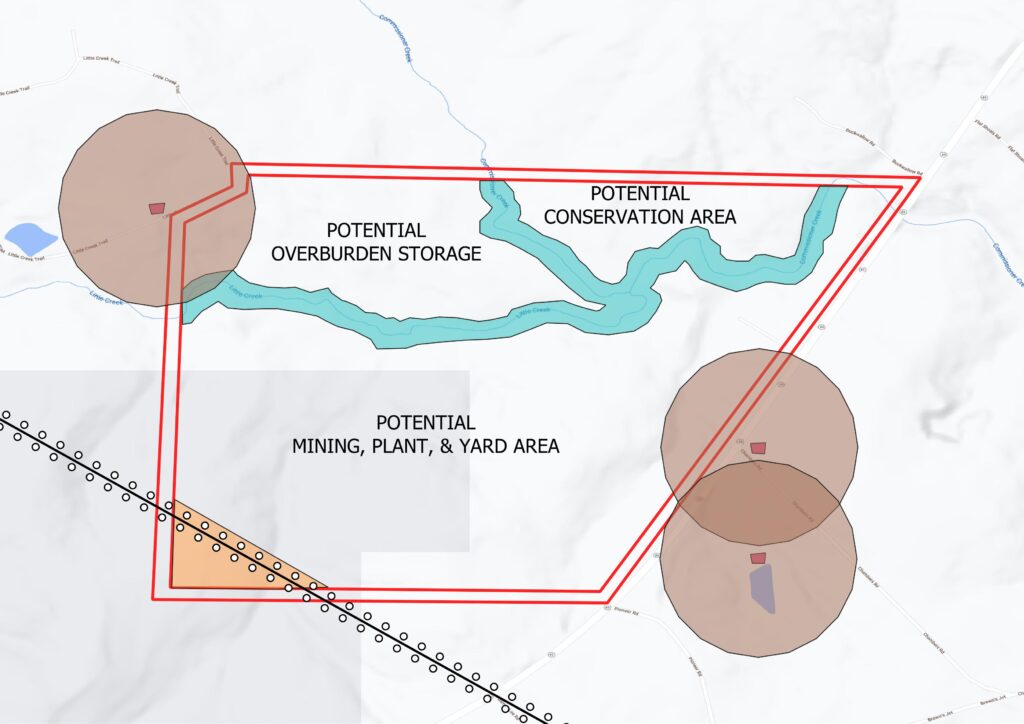
At this stage, the remaining area is considered safe and usable for mining purposes. But the evaluation doesn’t end here. You should also consider the parts of the site that were excluded by the blasting radii. While they can’t be used for mining, they can serve other purposes critical to the operation, such as stockpiling areas, plant locations, office space, and other non-mining related functions.
Moreover, if space is a concern, some of these areas can also be utilized for an “overburden pit”—a place for storing the unusable material stripped away from the pit or quarry during mining. As there’s typically no blasting involved in creating an overburden pit, it provides an opportunity to make use of areas closer to blasting buffers. But, keep in mind that when the operation hits rock, it should still remain outside the blasting buffers from structures.
Conclusion
Evaluating a greenfield site for its usable acreage is a complex yet fascinating process, blending careful environmental stewardship with strategic operational planning. This guide has provided an overview of the evaluation process, but every site presents unique challenges and opportunities. Therefore, site evaluation should be conducted with due diligence, considering local regulations, environmental concerns, operational needs, and long-term business goals. Ultimately, the key is to balance the pursuit of profitability with respect for the environment and community, turning a greenfield site into a sustainable and successful aggregate operation.
Burgex Mining Consultants and Mineralocity Aggregates can significantly streamline the process of selecting and qualifying greenfield sites. We offer valuable services and tools that can help you make informed decisions.
Burgex Mining Consultants bring our extensive industry experience and technical knowledge to the table. We provide comprehensive site evaluation services, from initial property assessment to mining engineering and final viability studies. Our team of experts can help you navigate the complexities of selecting the perfect greenfield site by analyzing various aspects such as local regulations, environmental considerations, and potential operational restrictions.
Mineralocity Aggregates is a cutting-edge platform that provides a wealth of valuable data at your fingertips. It allows you to visualize potential sites, analyze market data, evaluate competition, and much more. The platform is designed to facilitate the identification of opportunities and enhance strategic decision-making. With its comprehensive producer information and powerful data visualization tools, Mineralocity Aggregates truly puts the power of information in your hands.
Together, Burgex Mining Consultants and Mineralocity Aggregates provide a comprehensive solution to the challenges of greenfield site selection, offering both the professional guidance and the data-driven insights necessary to make confident, informed decisions.
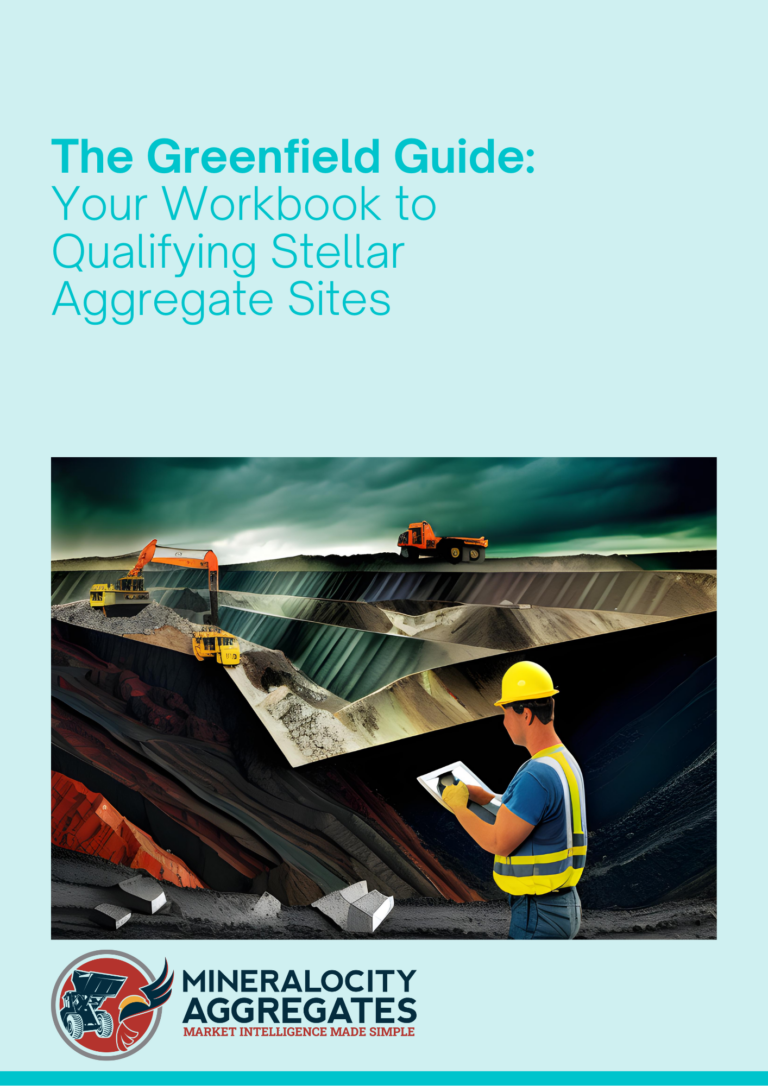
Ready to Unlock the Secrets of Successful Greenfield Site Evaluation?
Dive deeper into the world of construction aggregate production with our exclusive Greenfield Guide. Whether you’re a seasoned expert or just embarking on your aggregate adventure, this guide is your roadmap to identifying prime locations, assessing supply potential, and capturing significant market shares. Arm yourself with proven strategies, actionable insights, and essential formulas designed to propel your projects to unparalleled success. Don’t miss this chance to elevate your greenfield endeavors – grab your free copy of the Greenfield Guide now!