Navigating the complexities of the construction aggregate market can be daunting. One of the foundational elements to comprehend in this vast market is regional pricing. By grasping regional pricing trends, industry players can make more informed investment and operational decisions. This article provides a guide to determining basic regional construction aggregate pricing.
1. Understand the Basics of Aggregate Pricing
The price of construction aggregates isn’t just based on the material itself, but a combination of factors:
- Extraction costs: The cost to mine or extract the material.
- Processing costs: After extraction, the material must be processed to meet certain specifications.
- Transportation costs: How far the aggregate needs to travel to reach its end-user, especially given that transportation can constitute a significant portion of the total cost.
2. Local Supply and Demand
The basic economic principles of supply and demand play a pivotal role:
- Demand: Typically, regions with rapid urban development or infrastructure projects have higher aggregate demand.
- Supply: The availability of natural resources in the region, and the number of operational quarries or sand pits, will affect supply and, consequently, prices.
3. Study Previous Price Trends
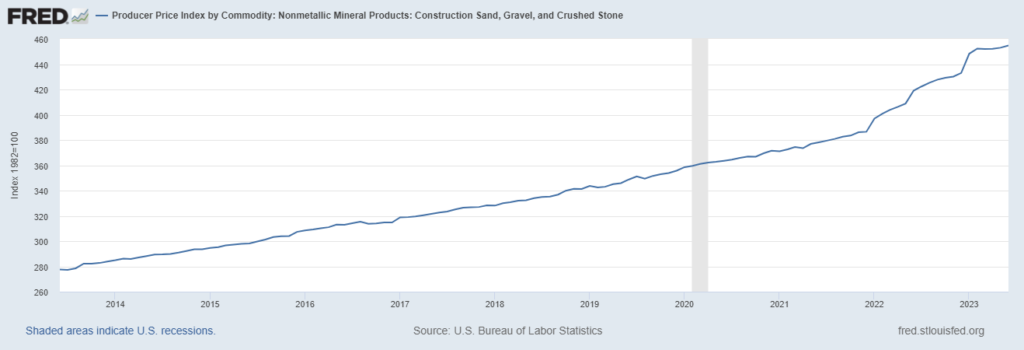
Look for historical data on aggregate pricing in the desired region. Organizations such as the USGS (U.S. Geological Survey) track wholesale pricing trends on a statewide level, providing invaluable data for those seeking to understand past pricing fluctuations. This can give insight into how prices have changed over time and provide a basis for future predictions.
4. Government Regulations & Taxes
Government policies can significantly impact the cost:
- Extraction licenses and permits: In some regions, it might be more expensive to get the necessary permissions to extract aggregates.
- Environmental regulations: Adhering to environmental guidelines might add to operational costs, which could be passed on to buyers.
- Taxes: Various taxes on mining operations or sales can affect pricing.
5. Quality of Aggregates
The quality and type of aggregate also play a role in its price:
- Grade: Higher quality or specialized aggregates generally command higher prices.
- Type: The demand for specific types of aggregates, such as granite, limestone, or sand, can vary regionally, impacting the price.
6. Competitive Landscape
Examine the number of competitors in the region:
- Monopoly vs. Competition: A single dominant supplier in a region might have different pricing dynamics compared to a region with multiple competing suppliers.
- Integration: Some suppliers might be integrated with construction companies, affecting how they price their products.
7. Consult Industry Reports and Experts
Industry reports often provide a wealth of data on regional pricing. Additionally, consulting with local industry experts or associations can offer insights that are not publicly available.
8. Utilize Technological Tools
Leveraging modern technology can provide dynamic insights into regional pricing. Platforms like Price-Bee have tools and expertise to help you develop a comprehensive pricing strategy. Mineralocity Aggregates also offers detailed regional supply and demand data, ensuring businesses remain updated with current market dynamics.
Conclusion
Determining basic regional construction aggregate pricing isn’t solely about crunching numbers. It requires a comprehensive understanding of the local market, competitive dynamics, government regulations, and more. By systematically assessing each factor and utilizing advanced tools and resources, businesses can gain a clear picture of the pricing landscape, ensuring they remain competitive and informed in their decisions.
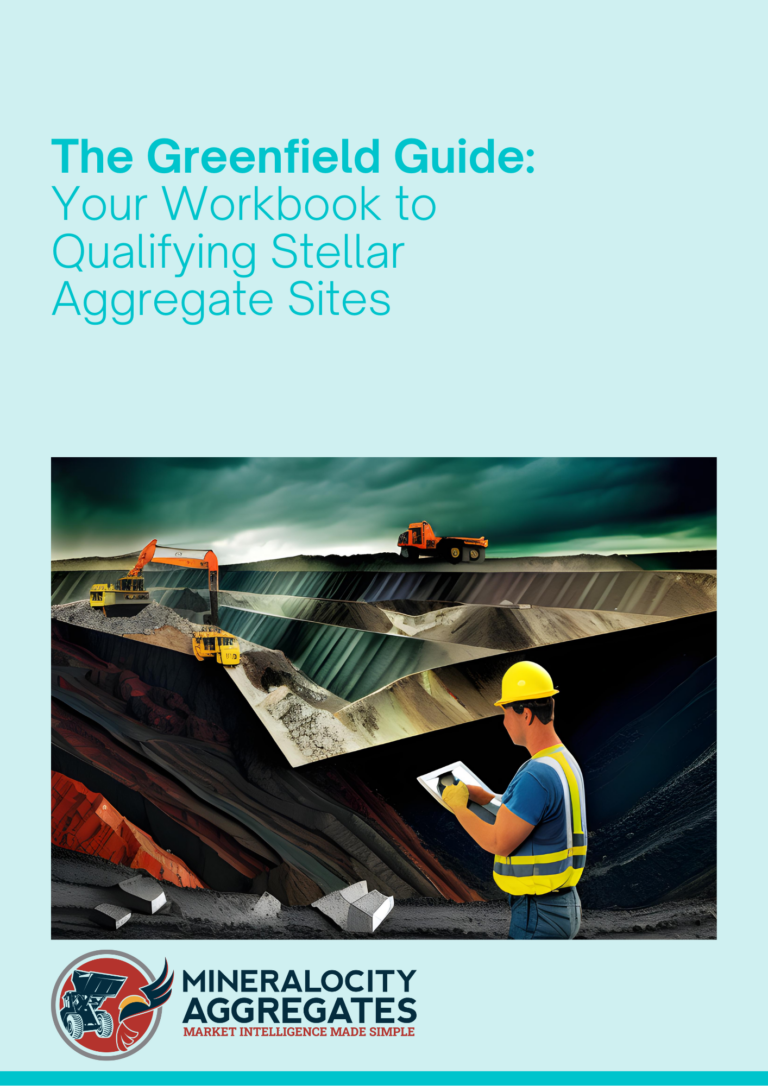
Ready to Unlock the Secrets of Successful Greenfield Site Evaluation?
Dive deeper into the world of construction aggregate production with our exclusive Greenfield Guide. Whether you’re a seasoned expert or just embarking on your aggregate adventure, this guide is your roadmap to identifying prime locations, assessing supply potential, and capturing significant market shares. Arm yourself with proven strategies, actionable insights, and essential formulas designed to propel your projects to unparalleled success. Don’t miss this chance to elevate your greenfield endeavors – grab your free copy of the Greenfield Guide now!