When seeking to start a new aggregate operation, one of the first questions a potential operator will ask is, “How much land do I need?” It’s an essential query that determines the scale, longevity, and feasibility of the project. While the specifics of land requirements can vary based on numerous factors, understanding some benchmarks is a good starting point.
Different Aggregate, Different Needs
The type of aggregate you’re planning to produce plays a significant role in determining the land requirements:
- Sand and Gravel Pits: These can generally be set up on a land area ranging from 40 to 160 acres. While it’s possible to fit a functional operation in the 40-acre range, it’s crucial to note that such a compact setup requires meticulous planning and optimization of space.
- Crushed Stone Quarries: These typically require more extensive land, somewhere between 80 and 320 acres. Crushed stone quarries often have substantial overburden that needs removal before reaching the valuable aggregate. This overburden demands space—not just for its storage, but also to ensure it’s managed in an environmentally and structurally sound manner.
The Overburden Challenge
Crushed stone quarries, as mentioned, often come with the challenge of more overburden. This loose, often unconsolidated material covering the aggregate can be a mixture of soil, clays, and smaller rock fragments. The presence of overburden isn’t merely an operational challenge; it’s also a spatial one. Overburden can’t be stacked indefinitely high due to its nature; it’ll naturally slope or spread out, consuming valuable land space.
Additional Land Considerations
While the numbers above provide a raw estimation of land size for actual extraction, several other components come into play:
- Processing Plants: Space for equipment, crushers, and possibly asphalt or concrete production.
- Stockpiles: Areas where the extracted aggregate is stored, waiting for transport or further processing.
- Settling Ponds: Essential for managing sediment-laden water and ensuring that the operation doesn’t harm the surrounding water quality.
- Scales and Administrative Buildings: Land to weigh outgoing trucks and manage the business aspect.
- Buffers and Boundaries: Creating buffer zones around your property can help in mitigating environmental impacts and reducing conflicts with neighbors.
- Environmental Safeguards: Wetlands, natural habitats, and other ecologically sensitive zones may need protection, which can reduce the usable land.
- Infrastructure: Access roads, utility lines, and other infrastructure can also consume space and need to be factored into the site’s overall design.
The Value of Meticulous Planning
Though it’s tempting to think in terms of just acreage, the real challenge and opportunity lie in planning. With careful mine planning, even a relatively smaller land area can turn into a highly productive and efficient aggregate site. Consider the entire lifecycle of the mine, from start to reclamation, and ensure the space can accommodate all stages. Additionally, leveraging modern technology, like Mineralocity Aggregates’ suite of tools, can aid in finding and creating an efficient and profitable operation.
Conclusion
The adage “more is better” holds some truth in the world of aggregate operations. While more land offers flexibility, scalability, and potentially a longer operational life, it’s also about what you do with the land you have. With the right planning, technology, and understanding of the requirements and challenges, both sand and gravel pits and crushed stone quarries can be designed to maximize efficiency, minimize environmental impacts, and deliver substantial profits, regardless of size.
Efficiency in site selection is often an amalgamation of thorough research, precise planning, and the right technological assistance. Mineralocity Aggregates excels in aiding this selection process with its comprehensive suite of tools. From its 30 basemap layers and detailed geology layers to the invaluable Regrid Nationwide Land Parcel data, Mineralocity offers capabilities that are tailor-made for the aggregate industry. Particularly noteworthy is the ability to filter land parcels to target sites that align with your specific acreage requirements. This level of precision and detail ensures that you’re always a step ahead in your greenfield site ventures.
Remember, the initial phase of assessing a potential greenfield aggregate site is just the beginning. As you delve deeper into the nuances of the site, leveraging specialized tools and expertise becomes not just advantageous but essential. In this regard, Mineralocity Aggregates stands as an invaluable partner, ensuring that your investment and efforts consistently bear fruit.
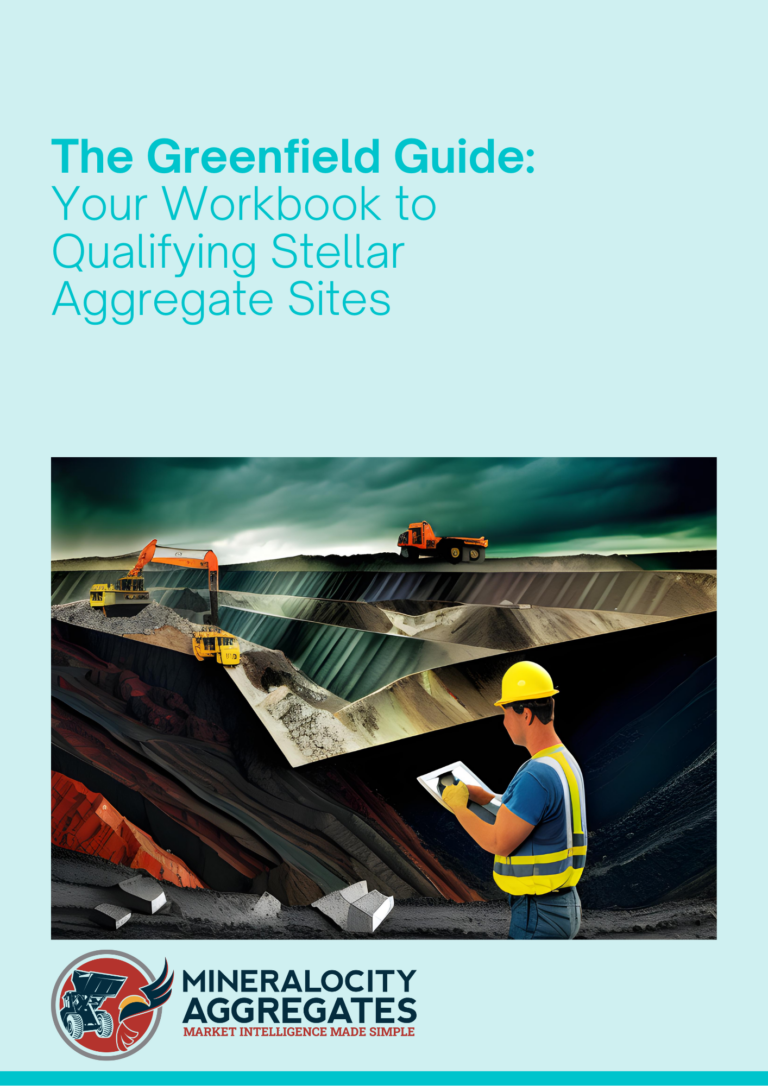
Ready to Unlock the Secrets of Successful Greenfield Site Evaluation?
Dive deeper into the world of construction aggregate production with our exclusive Greenfield Guide. Whether you’re a seasoned expert or just embarking on your aggregate adventure, this guide is your roadmap to identifying prime locations, assessing supply potential, and capturing significant market shares. Arm yourself with proven strategies, actionable insights, and essential formulas designed to propel your projects to unparalleled success. Don’t miss this chance to elevate your greenfield endeavors – grab your free copy of the Greenfield Guide now!