Introduction
The demand for construction aggregates—stone, sand, and gravel—serves as a powerful indicator of infrastructure investment, economic growth, and regional development across the United States. In 2024 and continuing through 2025, aggregate demand continues to reflect not only population trends but also large-scale transportation improvements, industrial expansion, housing pressures, and climate adaptation efforts. This analysis highlights the top 25 U.S. counties by estimated aggregate demand, revealing where construction activity is most concentrated and what types of projects are driving material consumption. From sprawling metros like Los Angeles and Houston to fast-growing inland hubs like Maricopa and Franklin counties, these regions represent the nation’s most intensive users of construction aggregates and point to the strategic role these materials play in shaping the built environment.
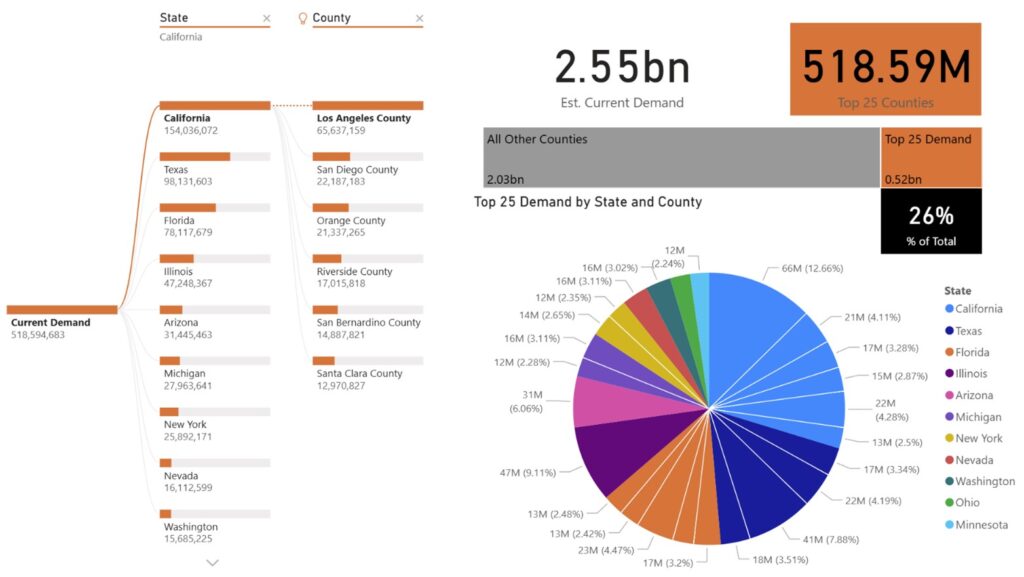
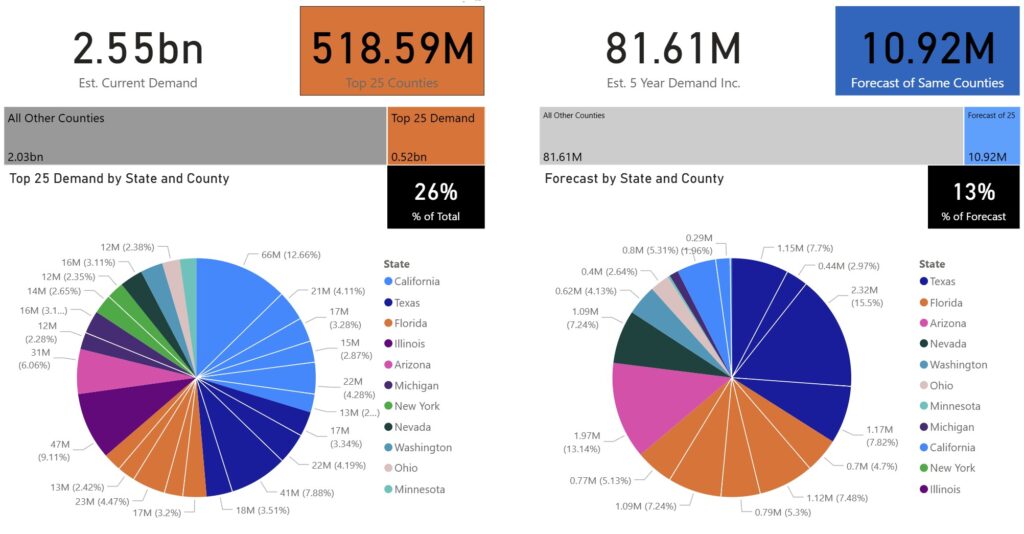
1. Los Angeles County, California
With an estimated aggregate demand of 65.6 million tons in 2024, Los Angeles County ranks as the top consumer of construction materials in the U.S. Its vast urban landscape demands consistent material use for highway maintenance, vertical redevelopment, port upgrades, and utility overhauls. Major investments include the I-405/Sepulveda Pass Expansion, bridge retrofits under Caltrans’ seismic resilience program, and modernization projects at LAX and the Ports of Los Angeles and Long Beach. Although demand is projected to decline by 1.8 million tons over five years, aggregate consumption remains high due to high-density infrastructure and continuous urban infill. Environmental permitting limits local sourcing, increasing reliance on long-haul imports from quarries in neighboring counties.
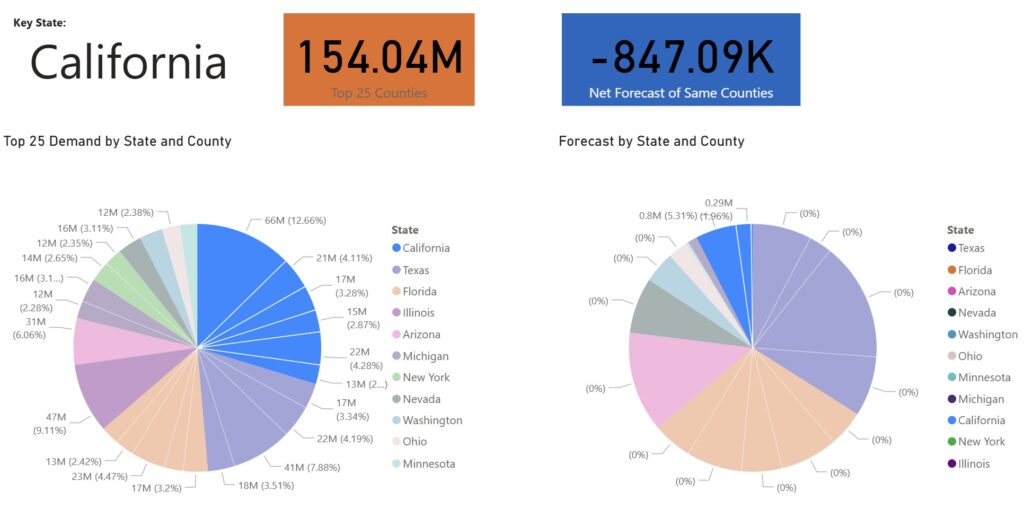
2. Cook County, Illinois
Cook County, home to Chicago, had an estimated demand of 47.2 million tons in 2024, ranking second nationwide. Key infrastructure projects such as the I-290 reconstruction, Red and Purple Line Modernization under the CTA, and the Chicago Region Environmental and Transportation Efficiency (CREATE) program sustain robust aggregate requirements. A projected decline of 1 million tons over five years is likely driven by increased vertical development, expanded recycling, and slower population growth. Despite this, the county’s aging infrastructure and expansive transit system continue to demand steady volumes of aggregate for maintenance and modernization.
3. Harris County, Texas
Harris County, which includes Houston, shows an estimated aggregate demand of 40.9 million tons in 2024, with a projected increase of 2.3 million tons by 2029. Demand is driven by expansive infrastructure projects including I-45 and I-69 freeway expansions, flood mitigation improvements, and Port Houston expansion initiatives. Industrial development and population growth in the Energy Corridor, Katy, and Cypress areas contribute to continuous subdivision and road construction. The county’s accessible supply chain—supported by regional quarrying—helps manage cost pressures and supports its status as a high-growth construction market.
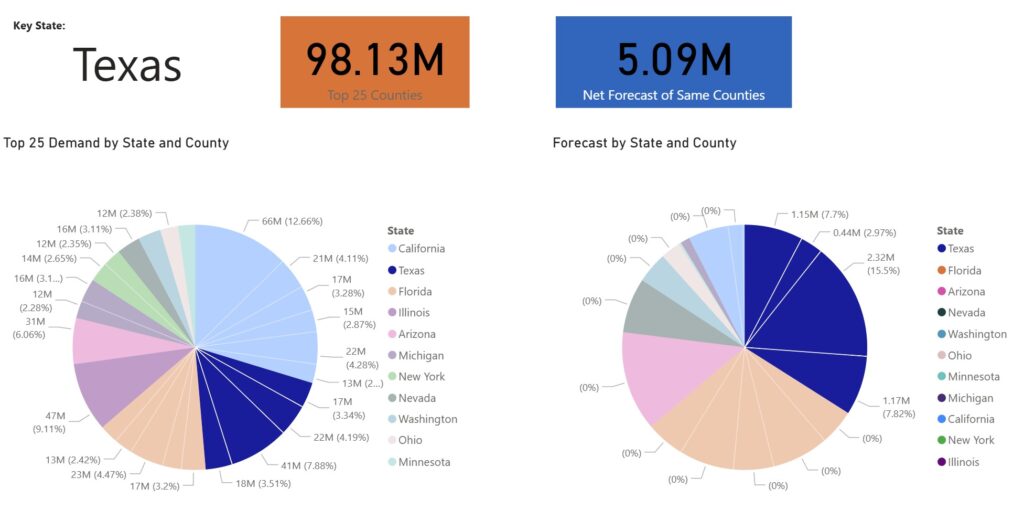
4. Maricopa County, Arizona
Maricopa County, encompassing Phoenix and its suburbs, has an estimated aggregate demand of 31.4 million tons in 2024, with a forecasted increase of 1.97 million tons over five years. Growth is fueled by freeway expansion projects such as the South Mountain Freeway, upgrades to Loop 202 and Loop 303, and the extension of the Valley Metro Light Rail. Rapid population growth in Buckeye, Queen Creek, and Surprise contributes to housing booms and commercial development. The presence of major tech facilities and data centers adds industrial-scale material demand, with consistent supply from nearby desert quarries keeping project timelines on track.
5. Miami-Dade County, Florida
Miami-Dade County’s estimated aggregate demand is 23.2 million tons in 2024, with a projected increase of 794,000 tons over five years. The county’s coastal position and vulnerability to flooding drive demand for climate adaptation and resiliency projects such as elevated roadways, seawall reinforcements, and the SMART Plan for bus rapid transit. Vertical redevelopment along the Biscayne corridor and institutional expansions (universities, hospitals) further sustain aggregate needs. With plentiful limestone sources nearby, Miami-Dade remains well-positioned to meet rising infrastructure and construction demands.
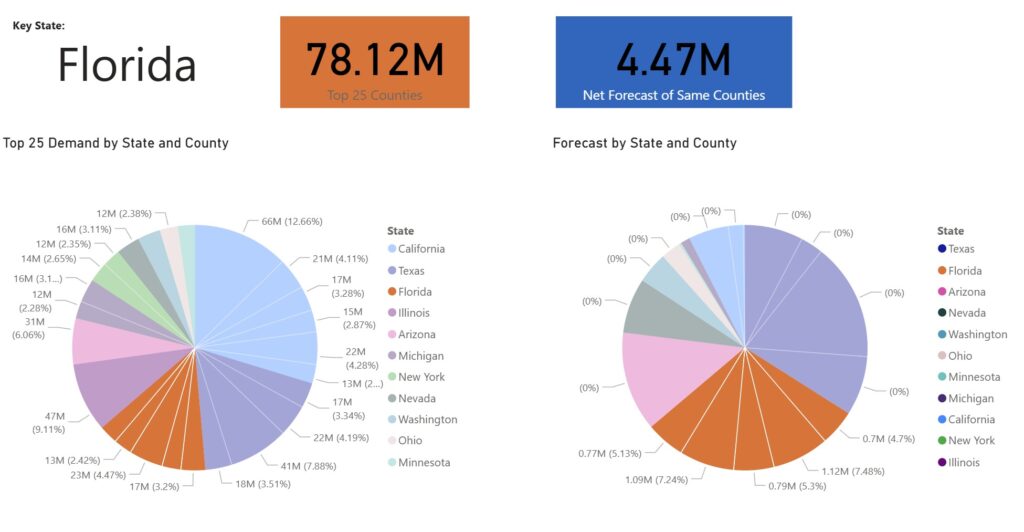
6. San Diego County, California
San Diego County has an estimated aggregate demand of 22.2 million tons in 2024, with a modest projected increase of 33,000 tons over the next five years. Demand is primarily driven by freeway upgrades, seismic retrofits, and military-related infrastructure near Camp Pendleton and the Naval Base. Major projects include improvements to SR-78 and I-5, Blue Line Trolley upgrades, and transit station redevelopment. Limited local quarry capacity means San Diego often relies on imported aggregate, raising cost sensitivity for developers and agencies alike.
7. Dallas County, Texas
Dallas County shows an estimated aggregate demand of 21.7 million tons in 2024, with an expected increase of 444,500 tons over the next five years. Ongoing projects such as the I-635 LBJ East Freeway expansion, Southern Gateway/I-35E corridor, and DART Silver Line rail system play significant roles. Continued population growth and urban infill in Garland, Mesquite, and Uptown Dallas support aggregate use for both vertical and low-density construction. Regional access to materials from North Texas quarries ensures consistent availability and supports rapid development timelines.
8. Orange County, California
Orange County has an estimated aggregate demand of 21.3 million tons in 2024, with a slight decline of 89,600 tons projected by 2029. Despite constrained growth, demand remains high due to projects like the I-405 Improvement Project, OC Streetcar, and civic building retrofits across Irvine, Anaheim, and Santa Ana. Environmental regulations and declining in-county production have pushed the region toward imports, particularly from the Inland Empire. This contributes to higher cost-per-ton metrics while maintaining high total demand.
9. Tarrant County, Texas
Tarrant County, which includes Fort Worth, posted an estimated aggregate demand of 18.2 million tons in 2024, with a projected increase of 1.17 million tons. Growth corridors along I-35W, Loop 820, and Alliance Airport see continued expansion in industrial logistics, residential developments, and airport-adjacent construction. TEXRail commuter extensions and mixed-use growth downtown help round out both public and private sector demand. Fort Worth’s access to nearby quarry resources keeps transportation costs low, supporting long-term development at scale.
10. Bexar County, Texas
Bexar County’s estimated aggregate demand was 17.3 million tons in 2024, with an increase of 1.15 million tons expected by 2029. Major public investments include the Loop 1604 expansion, I-35 NEX project, and flood mitigation infrastructure across the San Antonio River watershed. Joint Base San Antonio continues to drive federal demand, while private-sector housing, healthcare, and industrial facilities expand along the city’s north and west flanks. With local quarry access, Bexar remains cost-effective for high-volume aggregate distribution.
11. Riverside County, California
Riverside County had an estimated demand of 17.0 million tons in 2024, with an expected increase of 795,000 tons by 2029. It serves as one of the most active logistics and warehousing markets in the U.S., with industrial construction booming in Moreno Valley, Perris, and Jurupa Valley. Ongoing projects include the SR-60 truck lanes, I-215 interchange updates, and school modernization across the county. Though local quarries are present, environmental challenges and water access often limit production, increasing reliance on coordinated truck and rail shipments.
12. Broward County, Florida
Broward County has an estimated aggregate demand of 16.6 million tons in 2024, with a projected increase of 704,000 tons by 2029. Positioned between Miami and Palm Beach, the county supports sustained demand through a combination of coastal redevelopment, airport enhancements at Fort Lauderdale-Hollywood International, and resiliency infrastructure tied to sea-level rise. Projects like the I-595 express lanes, Port Everglades expansion, and drainage upgrades for hurricane season readiness require large volumes of fill and concrete. Urban infill in Coral Springs, Weston, and Pembroke Pines continues, while the county benefits from proximity to limestone producers in the Lake Belt region of South Florida.
13. Wayne County, Michigan
Wayne County, anchored by Detroit, has an estimated aggregate demand of 16.1 million tons in 2024, with a forecasted decline of 197,000 tons by 2029. While long-term population trends present challenges, major infrastructure investments provide stability. The Gordie Howe International Bridge, I-94 modernization, and upgrades to Detroit’s stormwater systems and freeway bridges are major contributors. Redevelopment of the downtown core and conversion of former industrial properties maintain moderate baseline demand. With minimal in-county aggregate production, material is sourced from southeastern Michigan quarries and often trucked in under tight urban constraints.
14. Clark County, Nevada
Clark County, which includes Las Vegas, has an estimated aggregate demand of 16.1 million tons in 2024, with growth projected at 1.08 million tons over five years. Construction activity remains robust thanks to resort expansions, professional sports infrastructure, Brightline West high-speed rail, and freeway upgrades along I-15 and I-11. Housing demand in Henderson and North Las Vegas continues, alongside commercial growth and energy infrastructure near Apex Industrial Park. Because of local geology, high-quality aggregate is often hauled in from central Nevada or southern Utah, requiring careful logistics planning for large projects.
15. King County, Washington
King County, including Seattle, has an estimated aggregate demand of 15.7 million tons in 2024, with a forecasted increase of 619,000 tons by 2029. Sound Transit’s Link light rail expansion, Alaskan Way Viaduct replacement, and ongoing seismic retrofitting support strong demand. Growth in Bellevue, Redmond, and the University District is anchored by tech campuses and multifamily redevelopment. The county’s limited local quarry supply necessitates barge or truck imports from Eastern Washington and British Columbia, increasing the cost-per-ton but sustaining high-volume demand in one of the nation’s densest metro areas.
16. San Bernardino County, California
San Bernardino County has an estimated aggregate demand of 14.9 million tons in 2024, with a projected increase of 294,000 tons by 2029. As part of the Inland Empire, the county continues to experience large-scale warehouse, distribution, and residential expansion across Ontario, Fontana, Rancho Cucamonga, and the High Desert. Infrastructure projects such as the I-15/I-10 interchange, rail freight improvements, and local flood control channel upgrades drive steady demand. With an abundance of permitted quarries and easier access to raw materials than neighboring coastal counties, San Bernardino serves as both a consumer and exporter of aggregates in Southern California.
17. Kings County, New York (Brooklyn)
Kings County (Brooklyn) has an estimated aggregate demand of 13.7 million tons in 2024, with a projected decline of 469,000 tons over the next five years. Despite the downturn, demand remains strong due to dense urban redevelopment, including NYCHA building modernization, seawall reconstruction, and street-level drainage retrofits. Most construction involves vertical reuse and infill, reducing per-project material volume but keeping steady demand from concrete-intensive mid- and high-rise structures. With no in-borough quarrying, all aggregate must be transported by barge or truck from regional sources, often at a premium due to limited staging and traffic constraints.
18. Santa Clara County, California
Santa Clara County, anchored by San Jose, has an estimated aggregate demand of 12.97 million tons in 2024, with a slight projected decline of 77,600 tons. Demand is anchored by large institutional developments, including BART Silicon Valley Phase II, hospital expansions, and retrofits of tech campuses in Cupertino, Sunnyvale, and Mountain View. Limited undeveloped land has pushed the market toward vertical mixed-use projects and public-sector transit and flood protection work. Local aggregate sourcing is limited by environmental regulation, driving up delivery costs for major projects across the county.
19. Hillsborough County, Florida
Hillsborough County, home to Tampa, has an estimated demand of 12.9 million tons in 2024, with a projected increase of 1.12 million tons over five years. Key drivers include I-275 widening, I-4 interchange modernization, and flood mitigation efforts linked to hurricane resilience. In addition to suburban housing expansion in Brandon, Riverview, and Lutz, the port district and medical campuses are undergoing long-term expansion. Proximity to aggregate sources in Central Florida makes sourcing cost-efficient, keeping local projects supplied for both private and municipal needs.
20. Palm Beach County, Florida
Palm Beach County recorded an estimated aggregate demand of 12.9 million tons in 2024, with a projected increase of 768,000 tons. Substantial demand arises from redevelopment along the Intracoastal Waterway, inland growth in Wellington and Royal Palm Beach, and coastal defense construction such as seawalls, dune replenishment, and flood control canals. Public school facility upgrades and westward residential expansion sustain a broad demand profile. The county benefits from quarry proximity in western Palm Beach and neighboring Hendry County, ensuring consistent supply for both inland and coastal projects.
21. Orange County, Florida
Orange County, home to Orlando, has an estimated aggregate demand of 12.5 million tons in 2024, with a projected increase of 1.08 million tons by 2029. Demand is driven by major transportation infrastructure like the I-4 Ultimate Project, SunRail commuter extensions, and the ongoing Orlando International Airport South Terminal expansion. Additionally, large-scale private developments such as Universal’s Epic Universe and resort corridor expansion along International Drive contribute to high-volume material needs. With residential growth in Lake Nona, Horizon West, and Winter Garden, the county’s infrastructure and housing sectors will continue to be material-intensive for the foreseeable future.
22. Franklin County, Ohio
Franklin County, anchored by Columbus, recorded an estimated aggregate demand of 12.3 million tons in 2024, with a projected increase of 395,000 tons over the next five years. The ongoing Intel semiconductor plant development in nearby New Albany is a significant driver, bringing major road expansions and utility infrastructure. Residential growth in the northwest suburbs, expansion of Ohio State University, and commercial logistics parks near Rickenbacker Airport contribute to continued demand. While much of the aggregate is locally sourced, rapid development timelines in the tech and logistics sectors may pressure supply chains.
23. Queens County, New York
Queens County has an estimated aggregate demand of 12.2 million tons in 2024, with a forecasted decline of 388,000 tons by 2029. Despite the decline, demand remains high from infrastructure priorities like the JFK Airport redevelopment, MTA subway accessibility upgrades, and stormwater management improvements. High-rise construction in Long Island City and affordable housing renovations throughout the borough drive concrete and subgrade needs. With no in-borough quarrying, all material is brought in by barge or truck, with strict delivery windows due to urban congestion and zoning limitations.
24. Oakland County, Michigan
Oakland County, located north of Detroit, shows an estimated aggregate demand of 11.8 million tons in 2024, with a projected increase of 183,000 tons. The county’s strong residential construction market, particularly in cities like Novi, Troy, and Rochester Hills, supports continuous low-rise development. Infrastructure projects include road widening under the Rebuilding Michigan initiative, upgrades to municipal water and sewer systems, and commercial projects in regional employment centers. Oakland County’s stable economic base and access to aggregates from southern Michigan pits help maintain long-term construction momentum.
25. Hennepin County, Minnesota
Hennepin County, which includes Minneapolis, has an estimated aggregate demand of 11.6 million tons in 2024, with a modest increase of 45,567 tons forecasted over five years. Major projects such as the Southwest Light Rail Transit, I-35W North MnPASS Express Lanes, and bridge replacements over the Mississippi River are the primary demand drivers. Downtown redevelopment, upgrades to University of Minnesota facilities, and climate adaptation infrastructure also play important roles. With material sourced from regional quarries in the Twin Cities metro area, Hennepin County benefits from consistent and relatively low-cost aggregate availability.
Conclusion
As evidenced by this ranking of top-consuming counties, aggregate demand is intrinsically linked to both the scale and diversity of regional development. Coastal counties such as Los Angeles, Miami-Dade, and San Diego show strong demand driven by dense infrastructure, port modernization, and climate-resilient construction. Meanwhile, high-growth inland regions like Harris, Maricopa, and Franklin counties are fueled by population migration, major tech investments, and highway expansion. Several counties, including Kings and Queens in New York, demonstrate how urban redevelopment can maintain steady demand even in land-constrained environments. Across all regions, local sourcing challenges, regulatory landscapes, and logistical dynamics also influence how aggregate materials are procured and delivered. Understanding these demand patterns not only informs producers and planners but also underscores the vital role aggregates play in building and maintaining the nation’s critical infrastructure.