Selecting the ideal greenfield site for a new aggregate operation is crucial for the long-term success and profitability of the venture. However, many investors and mining companies frequently stumble upon various pitfalls, some of which could be avoided with a well-thought-out strategy and thorough research. Let’s dive into some of the most common mistakes and how you can avoid them.
1. Underestimating Overburden
One of the primary challenges in setting up a new aggregate operation is managing the overburden, which is the non-commercial, unsellable material that overlays the target aggregate. Selecting a site with excessive overburden can dramatically increase start-up costs and delay production schedules. Before committing, always conduct a detailed geological survey to determine the volume and depth of overburden.
2. Navigating the Permitting Maze of Incorporated Areas
Areas that are incorporated or come under urban jurisdiction can be notoriously challenging for obtaining mining permits. Local governments, residents, and businesses may have concerns regarding noise, dust, traffic, and environmental impacts. Before selecting a site, it’s essential to understand the local regulations, potential opposition, and willingness of local authorities to grant permits.
3. Ignoring Site Obstacles
An ideal site on paper can quickly become a nightmare if it’s dotted with unmineable regions. Features such as wetlands, transmission lines, heritage sites, or protected habitats can segment the area, rendering vast portions of the land useless for mining. A detailed site survey, coupled with an understanding of local regulations, can help in avoiding these pitfalls.
4. Overlooking Market Research
The excitement of finding a site rich in aggregates can
sometimes overshadow the essential step of market research. Even a site with
abundant high-quality aggregates can fail if there’s no local demand or if the
competition saturates the market. A detailed market study, which includes
potential customers, competitors, and transportation costs, is essential.
5. Not Utilizing Advanced Tools for Site Analysis
In today’s digital age, several advanced tools can offer invaluable insights into site selection. Platforms like Mineralocity Aggregates provide comprehensive data layers, including geology, accessibility, infrastructure, and market analysis. Leveraging such tools can prevent costly mistakes and give investors a significant edge in site selection.
6. Neglecting Long-Term Planning
While a site might be lucrative for the short term, it’s vital to have a vision for the long-term viability of the operation. This includes considering factors like the potential for site expansion, evolving market trends, and future infrastructure developments that could impact the operation.
7. Underestimating Infrastructure Needs
Every mining operation requires robust infrastructure, both onsite (like roads within the site, processing plants, and waste management facilities) and offsite (access to major highways or rail lines). Underestimating these infrastructure needs can result in escalated transport costs and operational inefficiencies. Proper planning ensures aggregates can be moved efficiently from the mine to the market.
8. Neglecting Community Engagement
Even if a site is rich in aggregates and perfectly located, neglecting or underestimating the importance of community engagement can be detrimental. Engaging with local communities early on, understanding their concerns, and building trust can be crucial in obtaining permits and ensuring smooth operations. Local opposition can lead to costly delays or even project cancellations.
9. Overlooking Water Management
Water plays a significant role in aggregate operations, especially in dust control, processing, and rehabilitation of mined-out areas. Failing to account for water sourcing, usage, and discharge can lead to operational issues and potential conflicts with environmental regulations and local communities.
10. Failing to Plan for Rehabilitation
Every aggregate mining operation has an endpoint. Failing to plan for the site’s rehabilitation can not only lead to regulatory issues but also potential financial liabilities. Properly rehabilitating a site can also enhance a company’s reputation, making it easier to secure permits for future operations.
11. Ignoring Technological Innovations
The world of mining is constantly evolving, with new technologies offering better efficiency, safety, and environmental compliance. Failing to stay updated and ignoring these innovations can result in operational inefficiencies and a potential competitive disadvantage.
By being aware of these additional pitfalls and approaching site selection with a comprehensive, well-researched strategy, companies can ensure that their aggregate operations are not only profitable but also sustainable and harmonious with local communities and environments.
Conclusion
Finding the right greenfield site for aggregates is a complex process that requires a blend of geological, logistical, regulatory, and market knowledge. By being aware of common pitfalls and leveraging tools like Mineralocity Aggregates, investors can increase their chances of success and profitability. As always, it’s essential to remember that thorough research and consultation with experts can save significant time, money, and headaches in the long run.
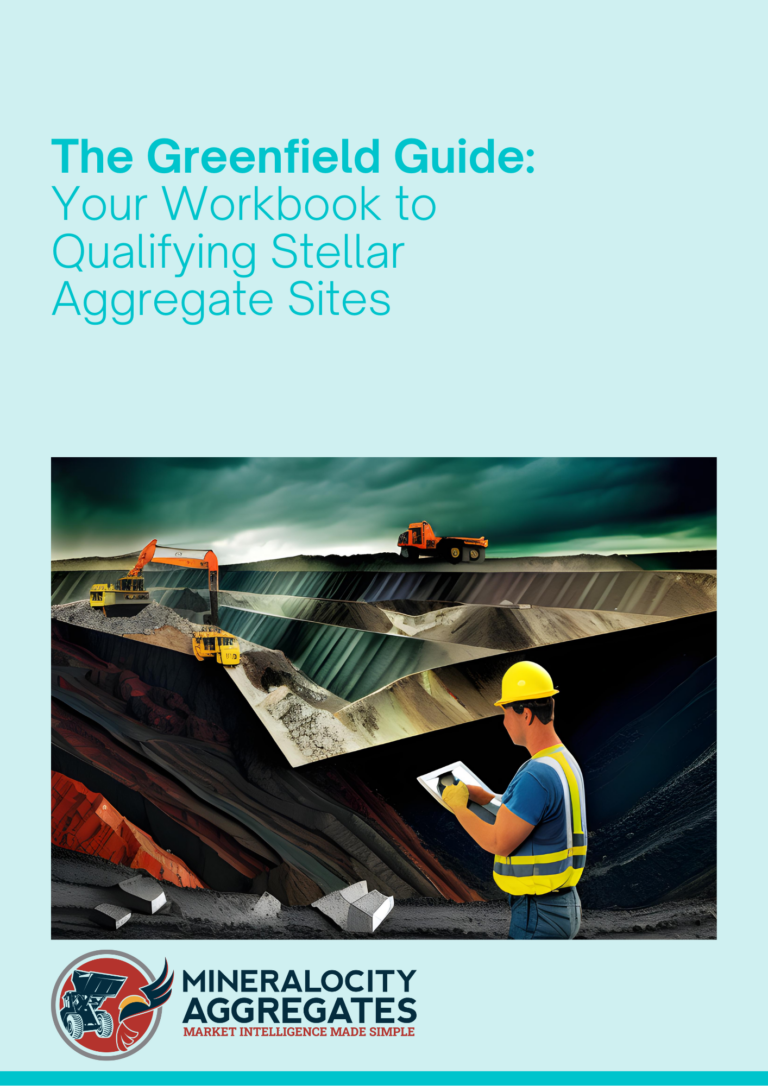
Ready to Unlock the Secrets of Successful Greenfield Site Evaluation?
Dive deeper into the world of construction aggregate production with our exclusive Greenfield Guide. Whether you’re a seasoned expert or just embarking on your aggregate adventure, this guide is your roadmap to identifying prime locations, assessing supply potential, and capturing significant market shares. Arm yourself with proven strategies, actionable insights, and essential formulas designed to propel your projects to unparalleled success. Don’t miss this chance to elevate your greenfield endeavors – grab your free copy of the Greenfield Guide now!